Las uniones fijas, son las fijaciones realizadas por soldadura o adhesivos estructurales, en las que se requiere cortar las piezas para su desmontaje y sobrecalentarlas en su nuevo ensamblado.
Este tipo de piezas, se debe tener en cuenta que la intervención sobre ellas es mas laboriosa y presenta mas dificultades, su empleo es necesario para conferir mas resistencia al vehículo.

Uniones fijas.
Dentro del grupo de uniones fijas podemos destacar la amplitud de las mismas en cuanto su disposición:
º Uniones a solape.
º Uniones a solape escalonado.
º Uniones a tope.
º Uniones a tope con resaltes.
º Uniones con refuerzos de bridas.
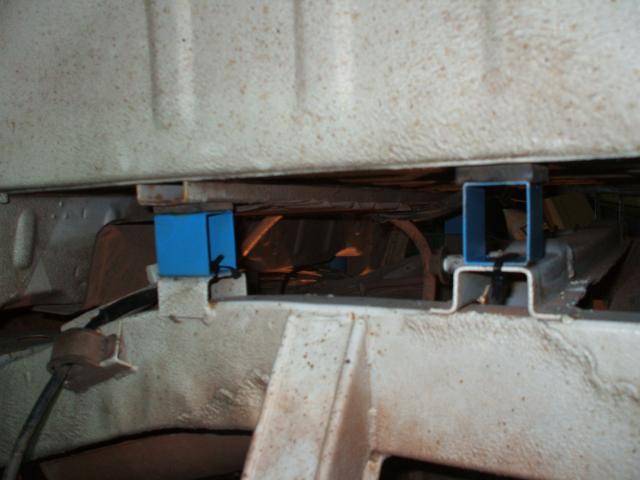
º Uniones engatilladas.

En cuanto a los métodos de unión, podemos encontrarlas:
-Pegadas
-Soldadas
Uniones pegadas
Existen tres tipos de adhesivos estructurales:
1) Adhesivos rígidos: de alta resistencia frente a esfuerzos normales o de cortadura. Baja resistencia frente a esfuerzos de pelado y desgarro. Mala resistencia frente a esfuerzos dinámicos e impacto.
1.1) Con gran capacidad de relleno de holguras: Epoxis
1.2) Superficies coincidentes: Cianoacrilatos.
2) Adhesivos tenaces: de buena resistencia frente a esfuerzos normales o de cortadura. Buena resistencia frente a esfuerzos de pelado y desgarro. Buena resistencia frente a esfuerzos dinámicos e impactos.
2.1) Con gran capacidad de relleno de holgura: Epoxis tenaces, Acrílicos UV y anaeróbicos UV, Acrilicos bicomponentes.
2.2) Con capacidad intermedia de relleno de holgura: Acrílicos de curado con activador, Anaeróbios estructurales.
2.3) Para superficies coincidentes: Cianoacrilatos tenaces.
3) Adhesivos flexibles: baja resistencia frente a esfuerzos normales o de cortadura. Alta resistencia frente a esfuerzos de pelado y desgarro. Buena resistencia frente a esfuerzos dinámicos e impactos.
3.1) Siliconas y Poliuretanos.
Características de los adhesivos estructurales
-Los adhesivos estructurales pueden sustituir, parcialmente, a la soldadura por puntos.
-En el encolado de metales, los adhesivos pueden comportarse en cuanto a calidad, con una soldadura y a menudo ofrecen una resistencia mayor.
-Alcanzan valores resistivos de 150 y 250 kg/cm2 a ser cortados.
Ventajas de los adhesivos
-Permiten la unión de materiales distintos.
.Se pueden unir metales con propiedades electroquímicas distintas, evitando la corrosión, la erosión por fricción y la corrosión por frotamiento.
-Distribución uniforme de la tensión: se minimiza el riesgo de rotura por fatiga al eliminarse tensioñes puntuales.
-Mejoran la estética del montaje.
-Ofrecen, en muchos casos, buenas propiedades de estanqueidad.
Desventajas de los adhesivos
-Presentan bajos valores mecánicos.
-Tienen una resistencia limitada a la temperatura.
- Poseen una resistencia limitada a ácidos fuertes y al fuego.
Clasificación de los adhesivos estructurales
Los mas empleados son:
º Poliuretanos bicomponentes (PUR 2K): en spoilers, molduras, etc
º Resinas epoxi: paneles.
º Adhesivos acrílicos.
º Silanos modificados
Uniones Soldadas
Se denominan uniones soldadas a las realizadas mediante el proceso de soldadura. Este proceso consiste en unir dos piezas empleando una fuente de calor hasta obtener su fusión, estableciéndose entonces la unión del metal fundido de las piezas y del material de aportación.
Los procesos de soldadura se pueden clasificar en:
º Heterogéneos
º Homogéneos
La soldadura heterogénea
Consiste en una soldadura que se realiza con piezas de distinta naturaleza.
Existen dos tipos de soldaduras heterogéneas:
- Soldadura blanda, se caracteriza por la utilización de un material con bajo punto de fusión, normalmente el estaño (150-230Cº).
- Soldadura fuerte, en esta, se proporciona un material que proporciona una unión mas fuerte pero sin llegar a fusionar las piezas. En automoción se utiliza el latón, que funde a 600 y 900Cº.
La soldadura homogénea
Es aquella que permite la unión rígida y permanente entre dos metales de la misma naturaleza, es decir, cuando esas dos piezas se unen con un aporte del mismo material.
Básicamente estas soldaduras se pueden clasificar en:
Soldadura oxigas
Oxiacetilénica
Soldadura eléctrica
Por arco de resistencia:
º Atmosférica controlada:
-TIG
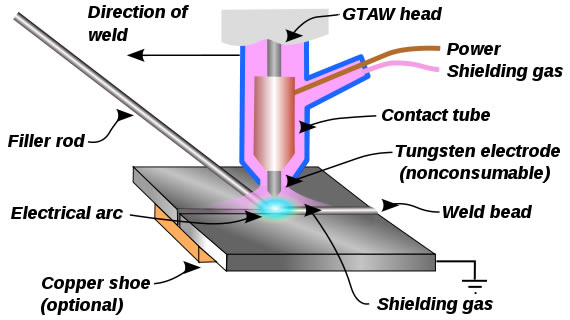
-MIG/MAG

-Láser
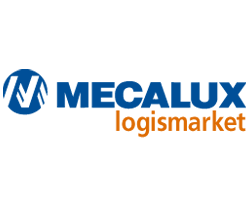
-Plasma

-Arco sumergido

-Haz de electrones
-Láser hibrido

º Atmósfera ambiental:
-Electrodo revestido

-SER
Procesos en función de la corriente empleada
Las maquinas de soldadura por salto eléctrico, utilizan transformadores y rectificadores, para funcionar en corriente continua y alterna, y poder disminuir o elevar su amperaje dependiendo de las características de lo que se valla a soldar.
Polaridad
Si observamos primero la CC, podemos elegir entre dos casos de polaridades diferentes, polaridad negativa y polaridad positiva.
La polaridad negativa cede la mayor parte de su energía a la pieza de trabajo, 70 %, de modo que obtenemos un baño de fusión profundo, con buena penetración. La carga sobre el electrodo es reducida, lo cual es una ventaja en la soldadura TIG. Una gran desventaja, al emplear esta polaridad es que el arco rompe la película de óxido, de modo que se impone un tratamiento previo de material, como la preparación cuidadosa de los bordes, limpieza muy cuidadosa y bordes biselados.
En combinación con arco pulsado se puede soldar chapa fina desde 0,06 mm. La soldadura con corriente continua y polaridad positiva (polaridad invertida) se usa para la soldadura MIG. Es típico que en la distribución de calor, el 70 % corresponda al electrodo. El baño de fusión es relativamente ancho y de escasa profundidad resultando en poca penetración.
Gas protector
Tanto el oxígeno como el gas combustible son alimentados desde cilindros, o algún suministro principal, a través de reductores de presión y a lo largo de una tubería de goma hacia un soplete. En este, el flujo de los dos gases es regulado por medio de válvulas de control, pasa a una cámara de mezcla y de ahí a una boquilla. El caudal máximo de flujo de gas es controlado por el orificio de la boquilla. Se inicia la combustión de dicha mezcla por medio de un mecanismo de ignición (como un encendedor por fricción) y la llama resultante funde un material de aporte (generalmente acero o aleaciones de zinc, estaño, cobre o bronce) el cual permite un enlace de aleación con la superficie a soldar y es suministrado por el operador del soplete.
La ventaja determinante para el uso de polaridad positiva consiste en el efecto rompedor de la película de óxido del arco, con tal eficacia, que dicha película ya no sea obstáculo para conseguir una buena calidad en la soldadura. El mecanismo para este efecto rompedor de la película de óxido no es completamente conocido, pero una explicación, es que se debe al bombardeo de la superficie de iones metálicos positivos análogo a la limpieza de superficies por chorreo.
Gas protector
Tanto el oxígeno como el gas combustible son alimentados desde cilindros, o algún suministro principal, a través de reductores de presión y a lo largo de una tubería de goma hacia un soplete. En este, el flujo de los dos gases es regulado por medio de válvulas de control, pasa a una cámara de mezcla y de ahí a una boquilla. El caudal máximo de flujo de gas es controlado por el orificio de la boquilla. Se inicia la combustión de dicha mezcla por medio de un mecanismo de ignición (como un encendedor por fricción) y la llama resultante funde un material de aporte (generalmente acero o aleaciones de zinc, estaño, cobre o bronce) el cual permite un enlace de aleación con la superficie a soldar y es suministrado por el operador del soplete.