Tipos de aleaciones no férreas en el automóvil
Las aleaciones mas frecuentes utilizadas en automoción son de metales pesados: Aleaciones de cobre ,de bronce, de níquel, de zinc, de estaño, de plomo y de aluminio.
Aleaciones de fusión cobre - zinc : son los
latones de fusión. Tienen mucha mas resistencia y mucha mas tenacidad que el
hierro fundido. Se emplean en casquillos de cojinetes (bearing
sleeves), guias de válvula (valve guides), resortes (springs)
Aleaciones de forja cobre - zinc : se obtienen
chapas o flejes por laminación en caliente o en frío de lingotes de fusión. Son
productos finales de cierta resistencia y alta dureza. Se emplea, por ejemplo,
en los tornillos calibrados del carburador (calibrated carburetor
screws), tubos (tubes) y recipientes de carga en radiadores y en intercambiadores
de calor (heat exchangers), intercooler, y tejidos de filtros (filters).
Bronces (bronzes):
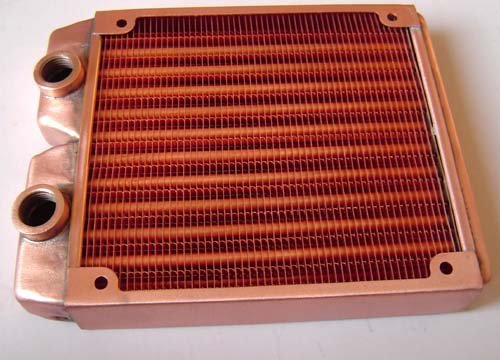
Aleaciones de fusión cobre - estaño : contienen
hasta un 15% de estaño. Muy resistentes al desgaste y al agua de mar. Se
emplean para casquillos de cojinetes (bearing sleeves), ruedas
helicoidales (helical wheels) y pistas de deslizamiento (sliding
tracks). Se conocen como bronces de máquinas.

Aleaciones de forja cobre - estaño : con éstas se
fabrican chapas (sheets), flejes, tubos (tubes), barras(rods),
y alambres (wire). Se emplea en resortes (springs), tubos
elásticos para manómetros (elastic tubes for pressure gauges), membranas (membranes)
y órganos de deslizamiento (organs of slippage).
Aleaciones cobre - plomo - estaño : presentan
excelentes cualidades de deslizamiento por lo que su empleo fundamentalmente se
sitúa en cojinetes (bearings), ya que el plomo proporciona buenas
propiedades de funcionamiento en condiciones críticas. Se suele encontrar en cojinetes (bearings)
y semicojinetes del interior del motor.
Aleaciones cobre - aluminio : poseen grandes
resistencias. Se presentan ideales para cojinetes (bearings) y
semicojinetes de alto grado de trabajo y choque. También son empleadas en ruedas
dentadas de mecanismos sin-fin (gearwheels).
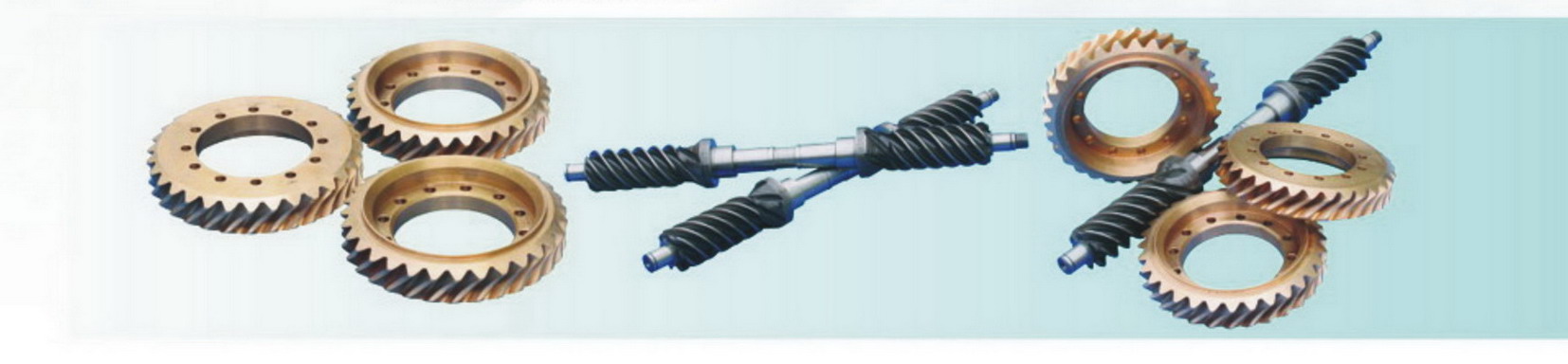
OTRAS ALEACIONES DE METALES NO FÉRRICOS
Aleación de cinc colado a presión con aluminio : se
conoce con el nombre de calamina. Es una aleación de reducidas propiedades
mecánicas, empleándose en carcasas de carburadores (housings
carburetors),bombas de combustible (fuel pumps), emblemas distintivos
de marcas (badges), manillas de puerta (door handles), etc.
Aleaciones de estaño : se aplican fundamentalmente para
soldadura blanda y rellenos en carrocería, conteniendo proporciones variables
de estaño del 12% al 90%, siendo el resto primordialmente plomo y después,
antimonio, bismuto o cadmio. sus características quedan reducidas a un
compendio de sus dos materias principales : el estaño y el plomo.